Oil mill owners: how to choose the right oilseed dryer
Struggling with inconsistent oil yield or quality? Hidden drying problems might be silently eating your profits. Master oilseed drying to unlock better results and protect your bottom line.
Yes, selecting the correct oilseed dryer is absolutely critical. It ensures optimal, uniform moisture removal. This directly improves oil extraction efficiency, prevents spoilage, preserves oil quality, and maximizes your overall yield and profitability.
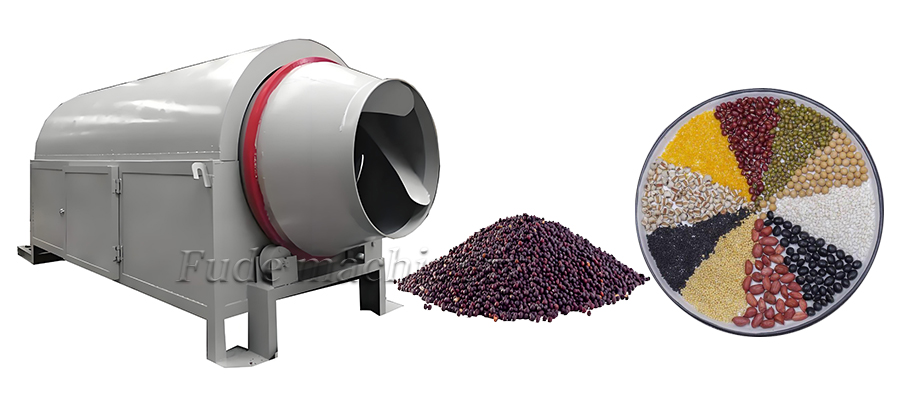
Common Mistake: Aggressive Single-Stage Drying
Using a high-temperature dryer (e.g., >100-120°C) directly on very wet seeds often causes:
- Case Hardening: The outer surface dries and hardens rapidly, trapping moisture inside (severe ‘false dryness’).
- Kernel Damage: Thermal shock can crack or damage the seeds.
- Oil Degradation: Exposure to high temperatures while moisture content is still high accelerates hydrolytic rancidity and oxidation.
- Inefficiency: Removing large amounts of water requires significant energy, and aggressive drying can be less energy-efficient overall.
Recommended Strategies for High Moisture
A multi-faceted approach is usually best for handling high-moisture oilseeds effectively and gently:
- Ambient Air Aeration / Pre-drying:
- Concept: Use large volumes of unheated or slightly heated (just above ambient) air blown through the seeds in a silo or bin.
- Goal: Safely remove initial free moisture down to a more stable level (e.g., 15-18%) without heat damage.
- Benefit: Low cost, minimizes quality degradation. Requires appropriate bins/silos with aeration floors/systems.
- Multi-Stage Drying:
- Concept: Use two or more drying stages with different temperatures, possibly with a tempering period in between.
- Example: Stage 1 at a lower temperature (e.g., 50-70°C) to remove bulk moisture. Stage 2 at a moderate temperature (e.g., 80-105°C) to reach the final target moisture. A tempering bin between stages allows moisture equalization.
- Benefit: More gentle on the seeds, better control, improved uniformity and quality compared to single-stage high-heat drying.
- Appropriate Dryer Types:
- Continuous Flow Dryers (Mixed-Flow, Counter-Flow): These are often designed with multiple temperature zones, allowing for a more gradual drying profile suitable for high moisture removal.
- Batch Dryers with Circulation: Recirculating batch dryers can provide good mixing and more uniform drying, suitable if continuous flow isn’t required.
- Key takeaway: Don’t rush the drying of very wet seeds. A staged approach is safer and more effective.
- Solution: For facilities regularly handling high-moisture seeds, investing in a combined system (aeration bins + multi-stage or multi-zone continuous dryer) offers the best long-term performance and quality preservation, despite potentially higher initial investment. Consult with experienced suppliers like us at Zhengzhou Fude Machinery to design a system suited to your climate and typical incoming moisture levels.
What’s the Smart Way to Choose a Heat Source and Optimize Airflow for Efficiency?
Drying is energy-intensive, significantly impacting your operating costs. Choosing the right heat source and ensuring the airflow system is properly designed are crucial for both cost-effectiveness and performance.
Select your heat source by balancing fuel cost/availability, environmental regulations, required temperature control precision, and safety. Indirect heating is strongly preferred over direct firing to prevent contamination. Optimize airflow by matching fan capacity (volume, pressure) to the dryer design and seed characteristics, using variable speed drives for flexibility and energy savings.
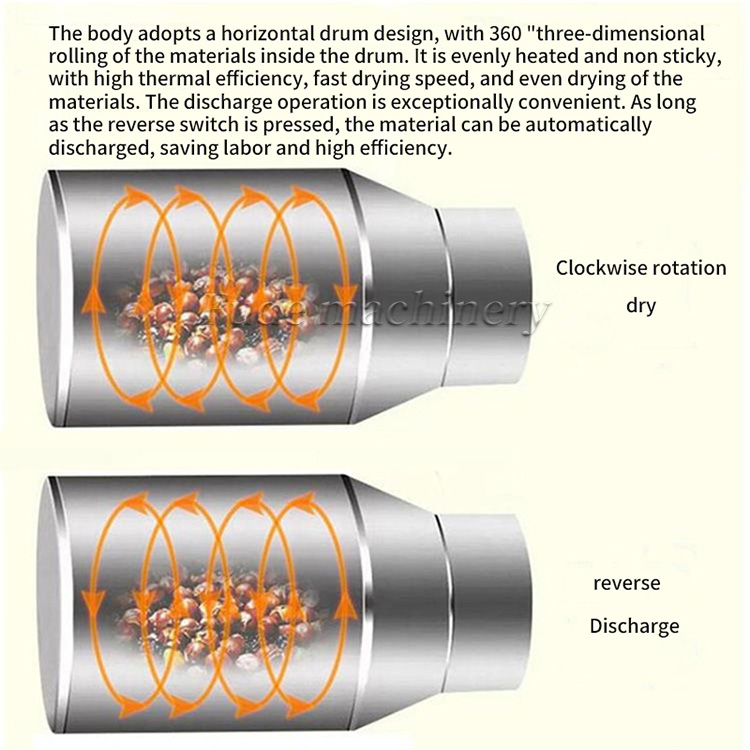
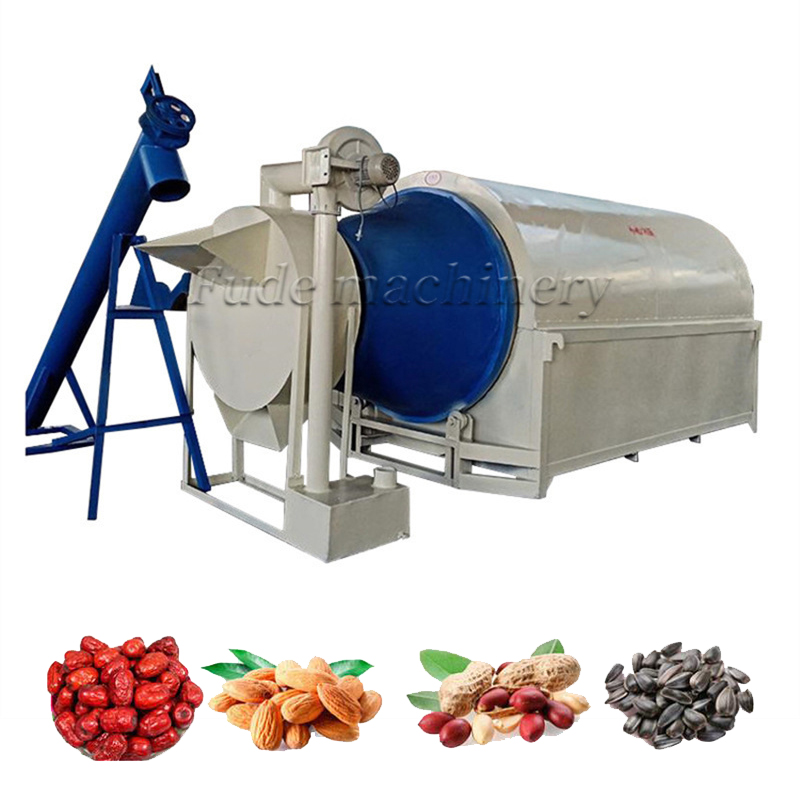
Making smart choices about how you generate and use heat for drying can save considerable money and ensure better operational control.
Selecting the Optimal Heat Source
The “best” heat source depends heavily on your location, scale, and priorities.
Heat Source | Pros | Cons | Considerations |
---|---|---|---|
Coal/Biomass (Direct Fired) | Lowest fuel cost (often) | High contamination risk (smoke, ash, carcinogens like Benzopyrene), poor temp control, pollution | Avoid for food-grade oil unless using indirect heat exchanger. |
Coal/Biomass (Indirect via Heat Exchanger) | Low fuel cost, Clean hot air | Higher initial cost, slightly lower thermal efficiency, requires maintenance | Good balance for cost & safety. Biomass is renewable. |
Natural Gas / LPG / Diesel (Indirect) | Clean hot air, Good temperature control | Fuel price volatility, requires fuel storage/supply infrastructure | Widely used, reliable, good automation potential. |
Steam (from Boiler) | Very clean, stable, excellent control | Requires existing boiler infrastructure, potentially high capital cost if new | Ideal if plant already has adequate steam capacity. |
Electric Heater | Most precise control, Very clean, simple setup | Highest operating cost (unless very cheap electricity) | Best for small scale, lab use, or high-value products where precision outweighs cost. |
- Key takeaway: Prioritize clean, controllable heat. Indirect heating is essential for food safety when using solid fuels.
- Solution: Perform a thorough cost-benefit analysis considering fuel prices, availability, maintenance, environmental compliance, and required control precision. For many, indirect biomass or natural gas offer a good compromise.
Beyond Specs: Are Maintenance, Supplier Support, and Future Needs Factored In?
Choosing a dryer based only on its listed capacity or initial price tag is shortsighted. You must also consider how easy it is to maintain, the reliability and expertise of the supplier, and whether the equipment can adapt to your future needs.
Neglecting maintenance access, supplier reliability, and future expansion needs leads to operational headaches, costly downtime, safety hazards, and limitations later. Plan for the long term by choosing wisely now.
Absolutely. Factor in ease of cleaning and maintenance by checking access doors, internal smoothness, and material choices (stainless steel contact parts are often worth it). Thoroughly vet the supplier’s industry experience, installation support, training, and after-sales service, including spare parts availability. Select equipment designed with potential for future upgrades, expansion, or integration with other systems.
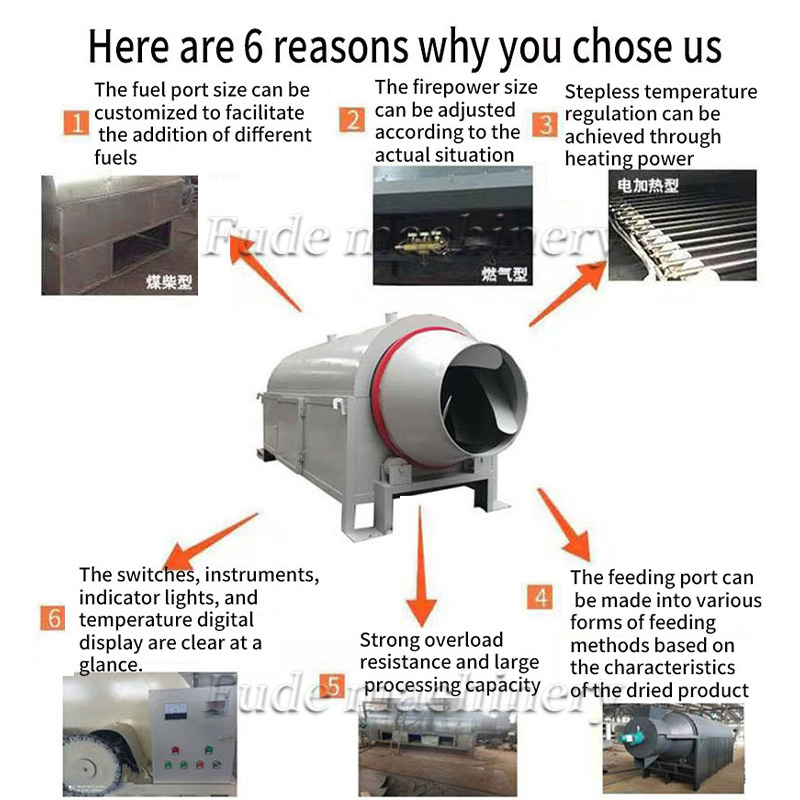
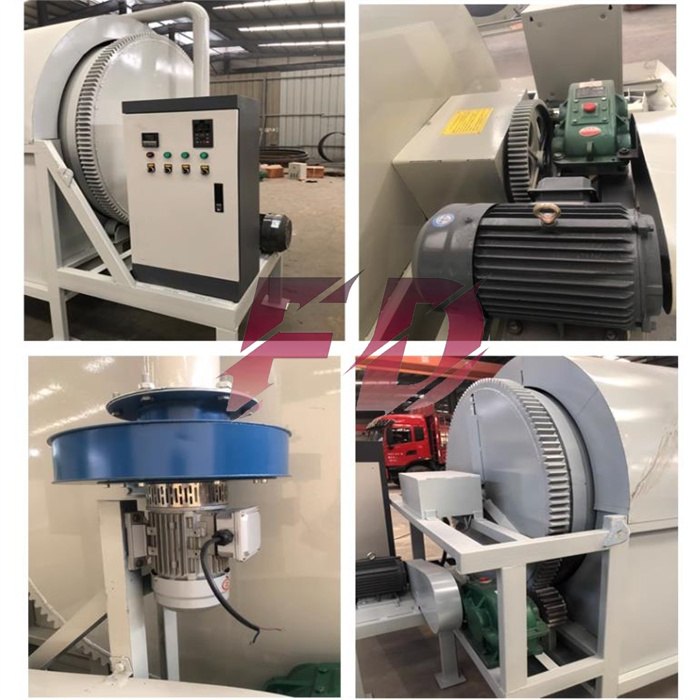
The long-term success of your drying operation depends on more than just the machine’s initial performance.
The ‘Hidden’ Costs of Poor Maintenance Design
Dryers inevitably accumulate dust, oil residue, and debris. A poorly designed machine makes cleaning and maintenance difficult and costly:
- Increased Labor: Hard-to-reach areas, too few or poorly placed access doors, and complex internal structures dramatically increase cleaning time and effort.
- Cross-Contamination: Residue left behind from one type of oilseed can contaminate the next batch, critical if processing different products or allergens.
- Fire & Explosion Risk: Oily dust accumulation is a serious fire hazard (spontaneous combustion) and can lead to devastating dust explosions if ignition sources are present. Easy cleaning is a safety feature.
- Reduced Efficiency: Clogged screens or air passages restrict airflow, reducing drying capacity and uniformity.
- Shorter Equipment Life: Neglected maintenance accelerates wear and tear.
- Key takeaway: Easy access and cleanable design save time, reduce risk, and improve performance.
- Solution: When inspecting potential dryers, specifically look for: ample, well-positioned access doors; smooth internal surfaces without unnecessary ledges or crevices; easily removable/cleanable screens or perforated plates; choice of materials (stainless steel for contact parts is highly recommended for cleanability and longevity).
Choosing the Right Partner, Not Just a Supplier
The company you buy from is as important as the equipment itself.
- Process Expertise: Does the supplier understand your specific oilseeds and the downstream pressing/refining implications? Can they provide sound advice on drying parameters?
- Installation & Training: Do they offer qualified technicians for proper installation supervision and comprehensive training for your operators and maintenance staff?
- After-Sales Support: How responsive is their service department? Do they stock critical spare parts (bearings, seals, screens, motors)? What are their warranty terms? Downtime is expensive.
- Customization Capability: Can they adapt the design to fit your site layout, integrate with existing lines, or handle unique material properties?
- Key takeaway: A good supplier is a long-term partner.
- Solution: Look for suppliers with proven experience in your sector (e.g., specific oilseeds you process). Ask for references and talk to their existing customers. Don’t just choose the cheapest option; evaluate the total value proposition including support and reliability. At Zhengzhou Fude Machinery, we pride ourselves on our deep process knowledge and comprehensive support.
Conclusion
Choosing the right oilseed dryer involves much more than comparing basic specifications. Consider moisture behavior, tempering effects, uniformity, operational challenges, energy use, maintenance, supplier reliability, and future needs. This careful evaluation is a vital investment for boosting your oil mill’s efficiency, quality, and long-term profitability. Make your choice wisely.
Related recommendations
-
What is the application prospect of grain dryer
174Grain dryers will play a more important role in the future
View details -
grain dryer
486What is a brewer's grain dryerThe characteristics of diesel fired grain dryersThe working principle of dryers grainSuitable materials for chicken manure dryerThe use effect of grain dryer platte sdThe advantages of a grain dryer clubroot acresDive...
View details -
Introduction to the Performance of Grain Drying Machine
236A grain dryer is a device used for drying grains. Its working principle mainly includes heating and drying, ventilation circulation, temperature control, humidity monitoring, and automatic dehumidification.
View details -
The effectiveness of using a vertical dryer
231Vertical dryers have demonstrated excellent performance in multiple fields due to their high efficiency, energy saving, uniform drying, easy operation, safety and reliability, wide applicability, and convenient maintenance
View details
HelloPlease log in