Can Ignoring Crude Oil Quality Ruin Oil Refining?
When Chemical Refining Works Best
Chemical refining, mainly using alkali to neutralize Free Fatty Acids (FFA), is the traditional method. It’s robust and adaptable. It works well even if your crude oil quality isn’t perfect or has high acidity. The process involves adding an alkali like caustic soda. This reacts with FFA to form soapstock, which is then removed, usually by centrifuges. This method effectively removes FFA and some other impurities. It’s a mature technology suitable for a wide range of crude oils like soybean oil or rapeseed oil. If your crude oil analysis shows high FFA or variable quality, chemical refining is often the safer, more reliable choice.
The Demands of Physical Refining
Physical refining removes FFA using steam distillation under high temperature and vacuum during the deodorization stage. It avoids the alkali process and soapstock formation, leading to lower refining losses. However, it demands much better preparation of the oil before deodorization. Gums (phospholipids) and color pigments must be reduced to very low levels in the degumming and bleaching stages. If the pre-treatment is not excellent, physical refining will not work well. It can lead to poor quality final oil. This method is best for oils that are naturally low in gums or for operations with very effective pre-treatment, like palm oil refining.
Making the Right Choice
So, the choice isn’t just about yield loss. It’s about matching the process to your raw material. We always ask for your crude oil analysis report. Key factors like FFA level and gum content guide our recommendation. Don’t choose physical refining just for the lower theoretical loss if your crude oil or pre-treatment capabilities aren’t suitable. That can lead to bigger problems and costs later. We help you evaluate this based on your specific situation.
Is Simple Hot Water Degumming Enough?
Simple water degumming only removes some gums (hydratable phospholipids). Non-hydratable gums remain, hindering later steps. Special degumming offers better results but costs more.
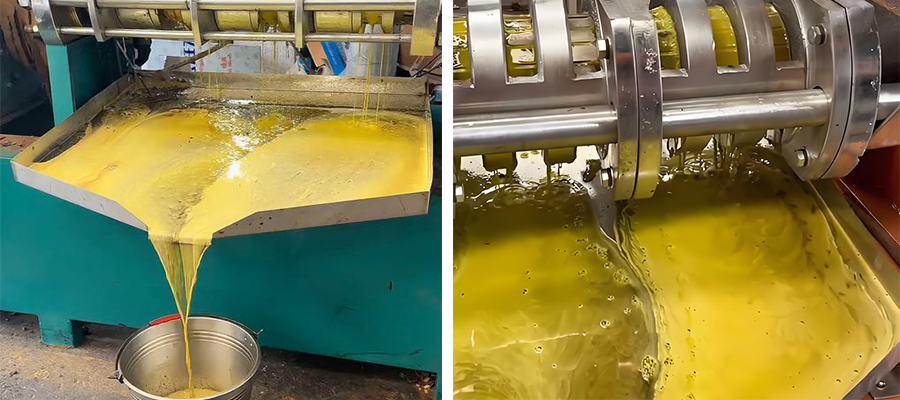
Degumming is often the first step in refining, and it’s more complex than it looks. Gums, mainly phospholipids, cause problems in later refining stages and affect final oil stability. Getting this step right is important for the entire process. Many think adding hot water is sufficient, but that’s often not the case.
Why is Deodorization So Critical and Energy-Intensive?
Struggling with off-flavors or low vitamin E? Poor deodorization is often the culprit. Understand this vital, high-energy step for quality oil production.
Deodorization removes FFA and odors using high temperature, vacuum, and steam. It heavily impacts flavor, stability, and nutrient retention. Proper equipment design is key.
Deodorization is usually the final stage in refining edible oils. Its main purpose is to remove undesirable substances that affect the oil’s flavor, odor, and stability. It’s arguably the most complex and energy-demanding step in the entire refining process. Getting it right is crucial for producing high-quality, bland, stable oil that meets market standards.
Goals of Deodorization
The primary goal is to remove Free Fatty Acids , especially in physical refining where this step replaces alkali neutralization. It also removes volatile compounds responsible for unwanted odors and flavors, such as aldehydes and ketones formed during oxidation. Additionally, deodorization can remove residual pesticides and other volatile contaminants. The process uses high temperatures (typically 200-270°C), high vacuum (very low pressure, 1-5 mbar), and injection of stripping steam. The combination of heat, vacuum, and steam helps these volatile substances evaporate from the oil.
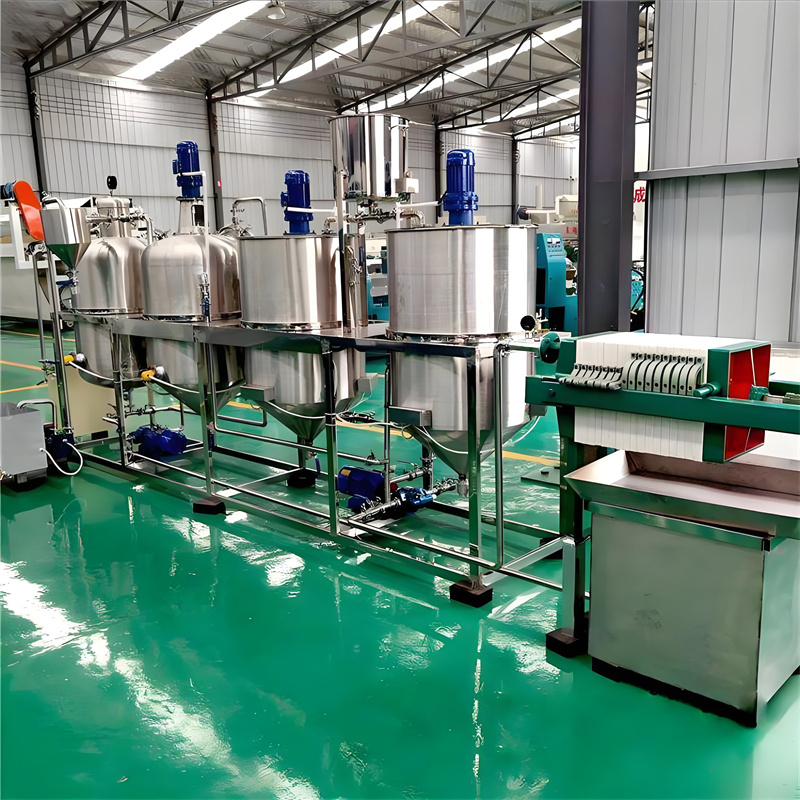
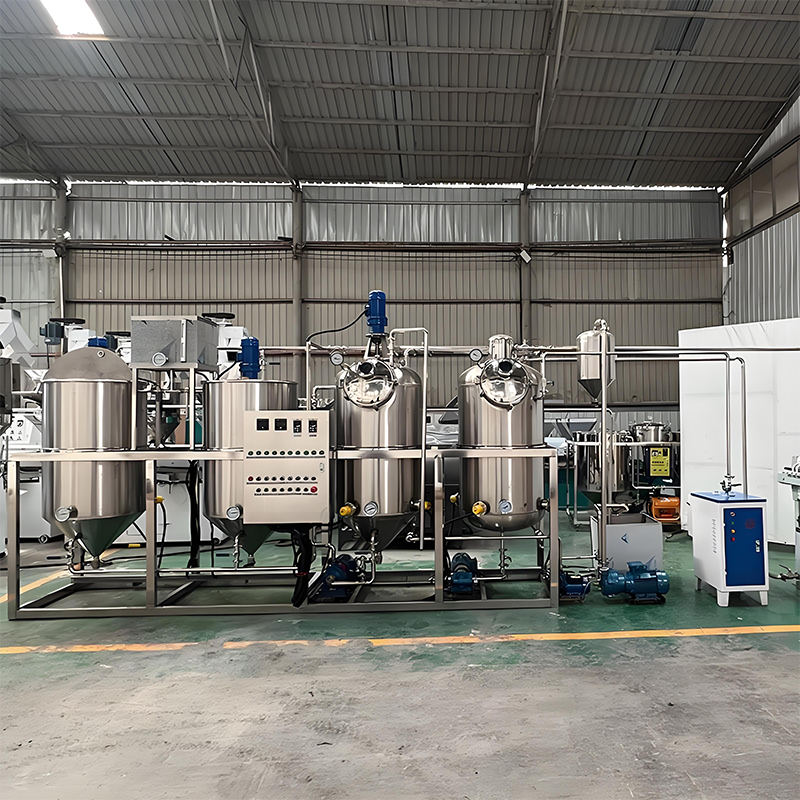
Critical Operating Parameters
Success depends on precise control of several key parameters:
- Temperature: High enough to volatilize FFA and odor compounds, but controlled to minimize damage to the oil and beneficial compounds like tocopherols. Excessive heat can also lead to the formation of undesirable trans fatty acids.
- Vacuum: A very high vacuum is essential. It lowers the boiling point of the substances to be removed, allowing them to evaporate at lower temperatures, thus protecting the oil quality. Maintaining a high vacuum requires efficient vacuum systems (steam ejectors or mechanical pumps).
- Stripping Steam: Direct injection of steam helps carry away the volatile compounds. The amount of steam must be carefully controlled – too little is ineffective, too much increases energy consumption and can lead to oil hydrolysis.
- Residence Time: The oil needs sufficient time in the deodorizer for the process to be effective, but not so long that heat damage occurs.
Equipment Design Matters
Deodorization consumes a lot of energy, mainly for heating the oil and generating steam and vacuum. Efficient equipment design is vital for effectiveness and cost control. Modern deodorizers often use structured packing or combined tray and packing designs inside a column. These provide a large surface area for contact between the oil and steam, improving stripping efficiency compared to older plate-type designs. Good design also incorporates heat recovery systems. Hot deodorized oil is used to preheat the incoming bleached oil, significantly reducing overall energy consumption. For small scale batch operations, achieving the necessary high vacuum and temperature control can be challenging, often leading to less effective deodorization compared to continuous systems. Investing in well-designed deodorization equipment, even for smaller scales, is important for final product quality.
Batch vs. Continuous: Which Refining Scale Fits Your Plant?
Starting small or scaling up your oil refining? Choosing the wrong equipment scale wastes money or limits growth. Match the system to your needs effectively.
Batch systems suit small volumes offering flexibility. Continuous lines are for larger volumes , providing efficiency and stability. Semi-continuous bridges the gap.
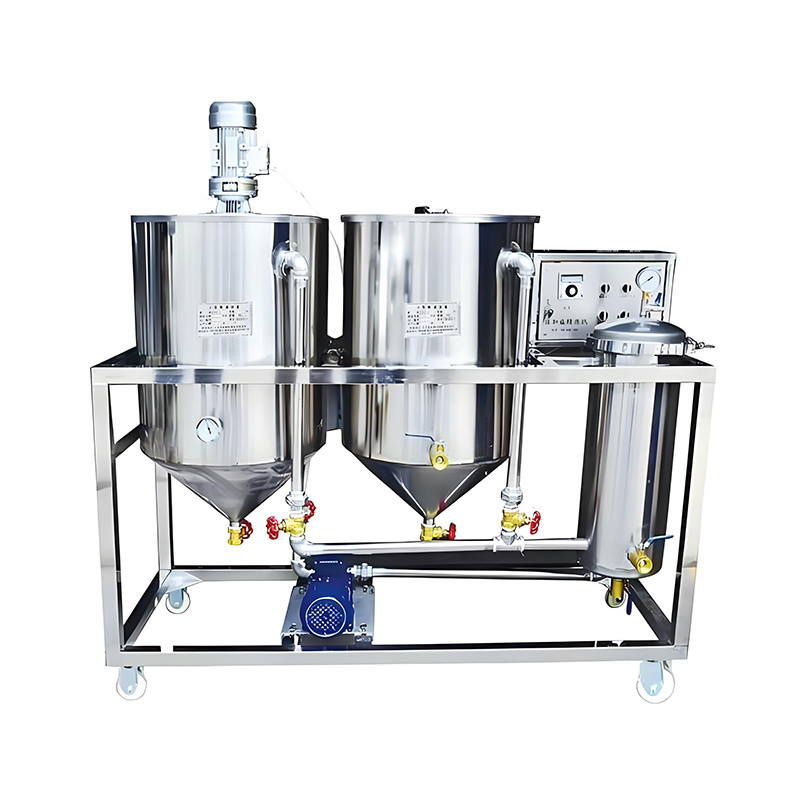
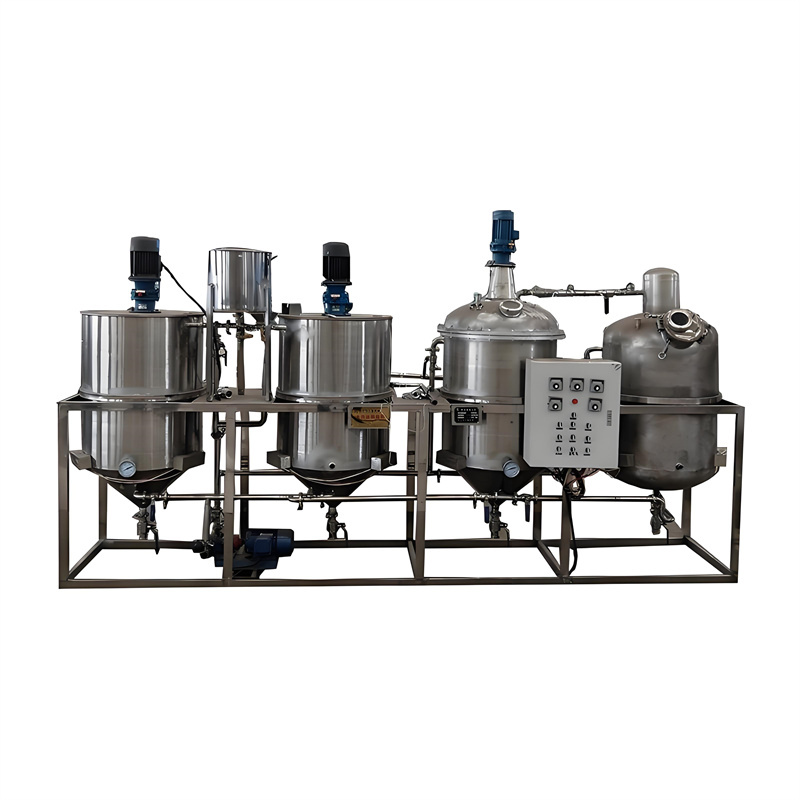
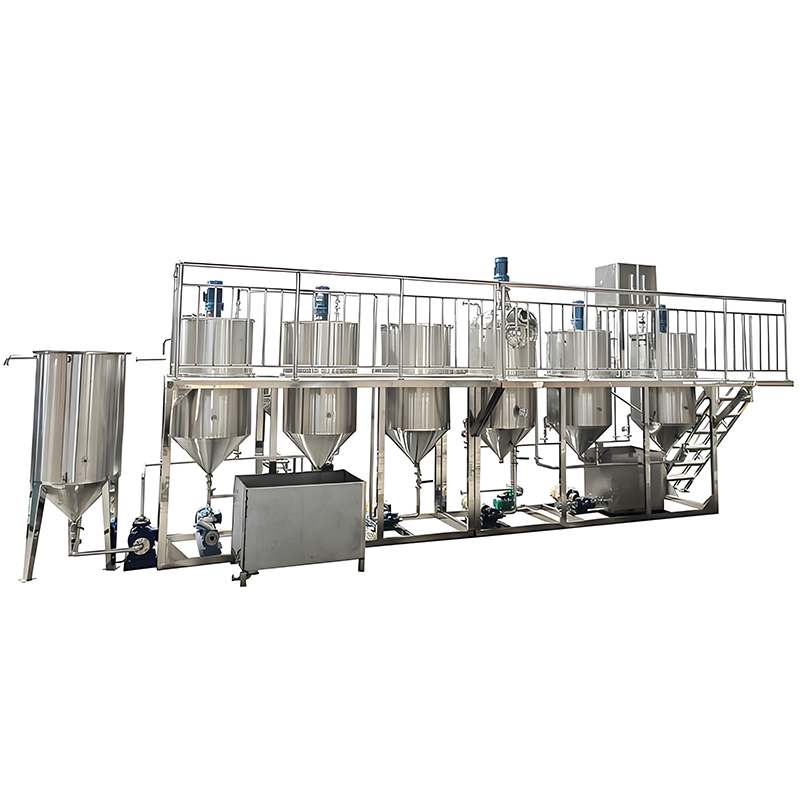
Choosing the right scale of refining equipment is a fundamental decision. It depends on your processing volume, budget, desired automation level, and operational flexibility. We offer solutions ranging from small batch systems to large fully continuous lines, and we help you determine the best fit.
Small Scale: Batch Refining
For smaller operations, typically processing from a few hundred kilograms up to about 10 tons of oil per day (TPD), batch refining is the most common choice. This system uses a series of tanks where each refining step (degumming, neutralizing, bleaching, deodorizing) is performed sequentially on one batch of oil at a time.
- Pros: Lower initial investment cost compared to continuous systems. More flexible for processing different types of oils or small quantities. Simpler operation in principle.
- Cons: Lower processing efficiency. Higher labor requirement per ton of oil. More variability in final product quality between batches. Often lower energy efficiency. Deodorization quality can be harder to achieve consistently due to limitations in vacuum and temperature control in basic batch setups.
We focus on providing high-quality batch systems, using food-grade stainless steel, efficient heating (like thermal oil), and reliable vacuum systems, even for small scales.
Medium Scale: Semi-Continuous Options
For processing capacities roughly between 10 TPD and 50 TPD, semi-continuous or smaller fully continuous lines become viable options. A semi-continuous setup might involve batch operations for degumming, neutralization, and bleaching, followed by a continuous deodorizer. This offers a balance between investment cost and operational efficiency. Small-scale continuous lines provide better consistency and efficiency than batch systems but require a higher investment. We can design modular systems that allow for future expansion. Key features at this scale often include centrifuges for separation and more automated control systems .
Large Scale: Fully Continuous Lines
For capacities above 50 TPD, and especially for operations processing hundreds of tons per day, fully continuous refining lines are the standard. In these systems, oil flows continuously through dedicated equipment for each step (e.g., degumming centrifuges, neutralization centrifuges, continuous bleaching towers, continuous deodorization columns).
- Pros: High processing efficiency. Stable and consistent product quality. Lower energy consumption per ton due to effective heat recovery. Lower labor cost per ton due to high automation.
- Cons: Very high initial investment. Requires skilled operators and maintenance personnel. Less flexible for frequent changes in oil type or small runs.
Designing a large continuous line is a complex engineering project that requires deep process knowledge and experience, which our team provides.
Regardless of the scale, we emphasize using quality components and sound process design to ensure the core refining steps are effective. Even a small batch plant needs a properly functioning deodorizer to produce good quality oil.
Labor, Maintenance, and Environment
The level of automation affects labor costs. Highly automated continuous plants require fewer operators per ton of oil compared to manual batch systems, offering long-term savings. Maintenance is another ongoing cost. Equipment built with high-quality materials (like proper grades of stainless steel) and components (pumps, valves, controls) will generally require less frequent and less costly maintenance. Consider the availability and cost of spare parts. Finally, environmental compliance is crucial. Treating and disposing of byproducts like soapstock and spent bleaching earth incurs costs. Processes that minimize waste or create more manageable byproducts can reduce these environmental expenses.
When evaluating proposals, look beyond the initial price. Ask suppliers about expected yield losses, utility consumption rates, and maintenance requirements. We provide detailed projections based on your specific needs, helping you understand the true lifetime cost of our solutions.
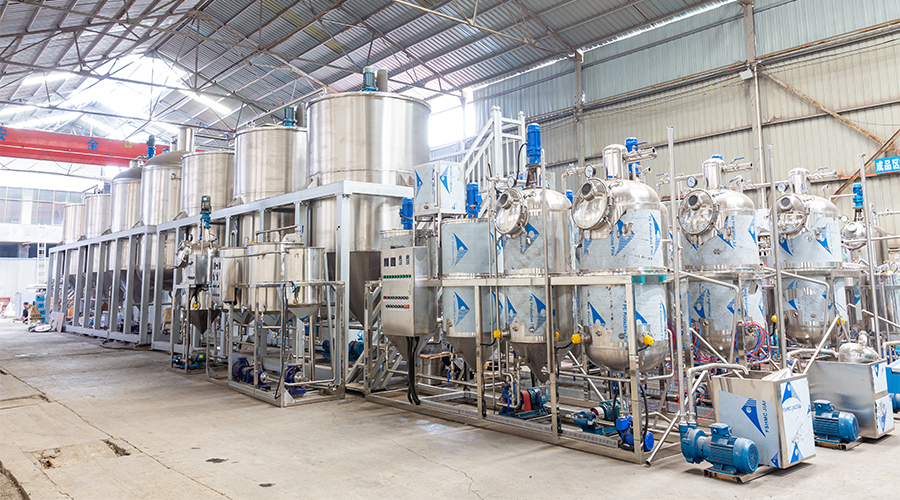
How Do You Choose a Reliable Refining Equipment Supplier?
Bombarded by equipment suppliers? Choosing the wrong partner means bad equipment and poor results. Learn how to select wisely for refining success.
Choose suppliers who understand your crude oil and target product. Look for process expertise, proven cases, quality manufacturing, and strong support, not just low prices.
Selecting the right supplier for your oil refining equipment is as important as choosing the right process. A good supplier is a partner who understands your needs and provides reliable technology and support. A bad choice can lead to equipment that doesn’t perform, poor quality oil, and endless frustration. As manufacturers with extensive experience, we know what buyers should look for.
What Information to Provide for a Custom Quote
To get a truly useful and reliable proposal, you need to provide potential suppliers with detailed information. The more they know, the better they can design a suitable solution. Be prepared to share:
- Crude Oil Type: Specify the source (e.g., soybean, rapeseed, sunflower, peanut, palm kernel) and extraction method (pressed or solvent extracted).
- Crude Oil Quality Analysis: Provide key parameters like Free Fatty Acid (FFA) content (or Acid Value), phospholipid content (gums), moisture, impurities, and initial color. This is critical.
- Target Finished Oil Quality: Specify the desired grade (e.g., National Standard Grade 1, specific customer requirements, export standards).
- Required Capacity: How many tons of crude oil do you plan to process per day (TPD)? Specify if this is based on 24 hours or a shorter working shift.
- Plant Conditions: Information about your available utilities (steam pressure/quantity, power supply, water quality) and factory space.
- Budget Range: Providing an approximate budget helps the supplier propose solutions within a realistic scope.
Choosing a supplier based on proven expertise, quality manufacturing, comprehensive service (design, installation, training, after-sales support), and a willingness to understand your specific needs is the best path to success.
Conclusion
Successful oil refining needs careful crude analysis and a tailored process. Choose partners who understand this for optimal results and profitability in your business.
Related recommendations
-
Oil mill owners: how to choose the right oilseed dryer
24Common Mistake: Aggressive Single-Stage DryingRecommended Strategies for High MoistureWhat's the Smart Way to Choose a Heat Source and Optimize Airflow for Efficiency?Selecting the Optimal Heat SourceBeyond Specs: Are Maintenance, Supplier Support...
View details -
Do you have any requirements for tea seeds for the tea seed peeling machine
153The requirements of the tea seed sheller for tea seeds mainly include maturity, dryness, cleanliness, consistency of specifications, and storage status
View details -
What can an oil press be used for
257An oil press is a machine used to extract oil from oilseed crops. It uses mechanical external force to increase the temperature to activate oil molecules, thereby squeezing the oil out of the oil.
View details -
What season is suitable for using the tea seed peeling machine
209The tea seed sheller is suitable for use during the season when tea seeds are ripe and have undergone appropriate pretreatment, mainly concentrated in autumn and other time periods after tea seed harvest
View details
HelloPlease log in