What key details are overlooked in screw presses?
Choosing a screw oil press seems straightforward. But hidden factors can sink your profits. We reveal what truly matters for success.
Understanding Pressing Temperatures
Friction is the main heat source. As the screw forces oilseeds through the confined space of the press chamber (barrel), intense pressure and material shearing generate significant heat. Even if no external heat is applied, continuous operation will raise the temperature of the oil and the machine components well above the ambient temperature.
- True Cold Pressing: Typically defined as keeping the oil temperature below 40-50°C throughout the process. This often requires very slow pressing speeds, specialized cooling mechanisms, or specific raw material conditions. It usually results in lower oil yield.
- Low-Temperature Pressing: What most commercial “cold press” screw machines achieve. Temperatures naturally rise due to friction, often settling between 60-80°C . This offers a balance between preserving some sensitive compounds and achieving acceptable oil yield.
- Hot Pressing: Involves deliberately pre-heating the seeds (cooking/roasting) before pressing, often to 100-130°C . This breaks down cell walls more effectively, significantly increasing oil yield but altering the oil’s flavor, color, and nutritional profile.
Why Temperature Control Matters
The actual temperature reached during pressing directly impacts the final oil quality. Excessive heat can degrade valuable antioxidants, vitamins, and polyunsaturated fatty acids. It can also alter the flavor and aroma profile. Therefore, knowing and controlling the actual operating temperature range is more important than relying on a “cold press” label. We help clients understand this and choose equipment, like our automatic temperature control presses, that offers the needed level of control for their specific oil type and quality goals.
Why is Raw Material Pre-treatment a Hidden Profit Center?
Focusing only on the press machine? Overlooking seed cleaning, cracking, or cooking? Discover how proper pre-treatment is key to maximizing oil yield and quality.
Effective pre-treatment is crucial. Cleaning removes impurities, adjusting moisture and temperature (especially via cooking/roasting) optimizes seeds for pressing, potentially boosting yield by several percent – directly impacting profit.
Many newcomers to oil pressing concentrate heavily on the specifications of the screw press itself. However, experienced operators know that what happens before the seeds enter the press is just as critical, if not more so, for achieving optimal results. Pre-treatment is where you gain a competitive edge.
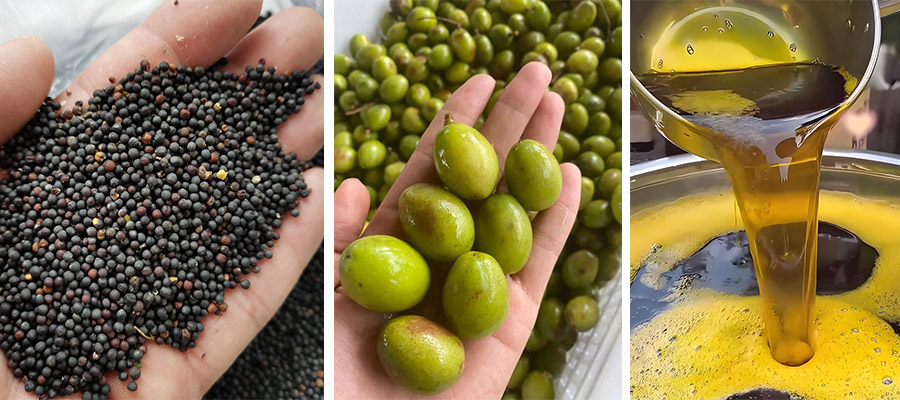
Key Pre-treatment Steps
The necessary steps depend on the oilseed type and desired final oil quality.
- Cleaning: Removing stones, sand, metal debris, leaves, and other foreign materials is essential. Impurities can damage the press, contaminate the oil, and lower the quality of the oil cake. We offer cleaning screens and destoners.
- Dehulling/Decorticating: Removing the outer shell (hull) for certain seeds like sunflower or cottonseed. Hulls absorb oil and increase wear on the press. Specialized dehulling machines are used.
- Cracking/Flaking: Breaking down larger seeds (like soybeans or palm kernels) into smaller pieces or flakes increases the surface area, making oil extraction easier and more efficient. Roller mills or flakers are common.
- Cooking/Roasting (Conditioning): This is arguably the most critical step for hot pressing. It involves carefully heating the prepared seeds to adjust moisture content and temperature.
The Importance of Cooking/Conditioning
Proper cooking does several things:
- Adjusts Moisture: Reduces moisture to the optimal level for pressing (typically 5-8%, varies by seed). Too wet, and oil flows poorly; too dry, and friction increases excessively.
- Ruptures Oil Cells: Heat helps break down cell walls, making the oil easier to release under pressure.
- Reduces Oil Viscosity: Warmer oil flows more easily.
- Coagulates Proteins: Helps in forming a firm press cake.
The right cooking temperature and time (“the art of cooking”) are learned through experience and vary significantly between oilseeds. Mastering this process, often using equipment like our drum or vertical cookers with precise temperature control, can directly increase your oil yield by valuable percentage points compared to competitors who neglect it. This difference goes straight to your bottom line. As a full-service provider, we guide clients on optimal pre-treatment for their specific needs.
Is “Pressing Until Dry” the Best Strategy for Screw Presses?
Aiming for the absolute lowest residual oil in the cake? Believing one pass should extract everything? Reconsider this common misconception for better efficiency and quality.
No screw press achieves 100% extraction. Pushing for extremely low residual oil (<5%) drastically increases wear, energy use, and heat, potentially damaging oil quality. A balanced residual oil level (6-10%) is often more economical.
It’s a natural desire to extract every possible drop of oil from your valuable raw materials. However, the pursuit of near-zero residual oil in the press cake using only a screw press is often counterproductive from both an economic and a quality standpoint.
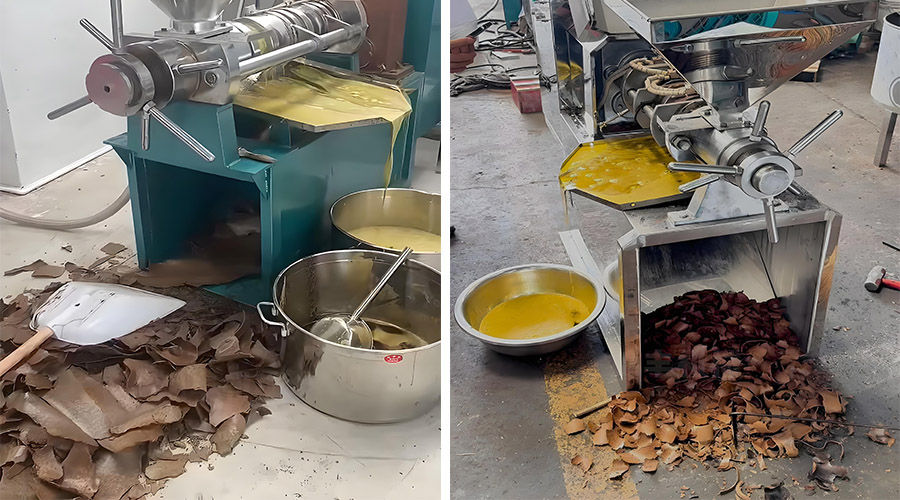
Matching Equipment to Scale
Different scales of operation benefit from different types of equipment:
Operational Scale | Typical Needs | Recommended Equipment Approach (Examples from Fude) |
---|---|---|
Small Business/Start-up | Low initial cost, ease of use, reliability | Single Screw Press (e.g., Auto Temp Control Models) |
Medium Oil Mill | Scalability, balance of cost & efficiency, some automation | Modular lines, robust Single or Double Screw Presses |
Large Industrial Plant | High throughput, automation, continuous operation | Fully integrated Pre-treatment, Pressing, Refining Lines |
As manufacturers offering a wide range from single presses to complete, customized lines, we emphasize working closely with clients to select equipment that truly fits their current needs and future growth plans, ensuring practicality and cost-effectiveness over unnecessary complexity. |
Does Good Oil Quality Come Straight from the Press?
Assuming the oil flowing out of the press is ready for bottling? Believing “cold pressed” means no further processing needed? Understand that post-press treatment is nearly always required.
Oil directly from a screw press (“crude oil”) contains impurities like fines, phospholipids, and moisture. At minimum, settling and filtration are needed for clarity and stability, even for “cold pressed” oil. Further refining is essential for higher grades.
A common misunderstanding, especially for those new to oil production, is that the oil exiting the screw press is the final product. While the press extracts the oil, the resulting liquid, known as crude oil or raw oil, requires further steps to become a stable, clear, and marketable product.
What’s in Crude Oil?
Even oil produced under optimal conditions contains various non-oil components:
- Fine Solids: Microscopic particles of the seed material that pass through the press cage gaps. These cause cloudiness and will settle over time.
- Phospholipids (Gums): These compounds absorb water and can lead to cloudiness and sediment, especially when heated (like during cooking).
- Free Fatty Acids (FFAs): Affect the oil’s acidity, flavor stability, and smoke point. Levels vary based on seed quality and processing.
- Moisture: Small amounts of water can reduce shelf life and clarity.
- Pigments: Natural color compounds (like chlorophyll, carotenoids).
- Waxes (in some oils like sunflower): Can cause cloudiness when the oil is cooled.
Essential Post-Press Steps
The level of processing required depends on the oil type and the target market quality.
- Settling (Sedimentation): Allowing the crude oil to sit undisturbed in tanks allows heavier solids and some moisture to settle to the bottom. This is a basic first step.
- Filtration: Removing suspended solids is crucial for clarity and stability. Common methods include:
- Plate and Frame Filter Presses: Use filter cloths/papers to trap solids. Effective and widely used. We manufacture various filter types.
- Centrifugal Separators: Use high speed to separate solids and potentially water.
- Bag Filters: Simpler method for lower volumes.
- Refining (for Higher Quality Grades): To meet national standards (like Grade 1 or 2) or specific customer requirements, a full refining process is necessary. This typically involves:
- Degumming: Removing phospholipids (gums).
- Neutralizing: Removing Free Fatty Acids (FFAs).
- Bleaching (Decolorizing): Removing pigments using bleaching earth.
- Deodorizing: Removing volatile compounds affecting taste and odor using steam under vacuum.
- (Optional) Winterizing: Removing waxes to prevent clouding at low temperatures.
We offer complete refining solutions, from small batch systems to continuous plants, ensuring our clients can produce oil that meets their specific market demands, going beyond just the initial pressing stage. Planning for filtration and potentially refining from the start is vital for a successful oil processing venture.
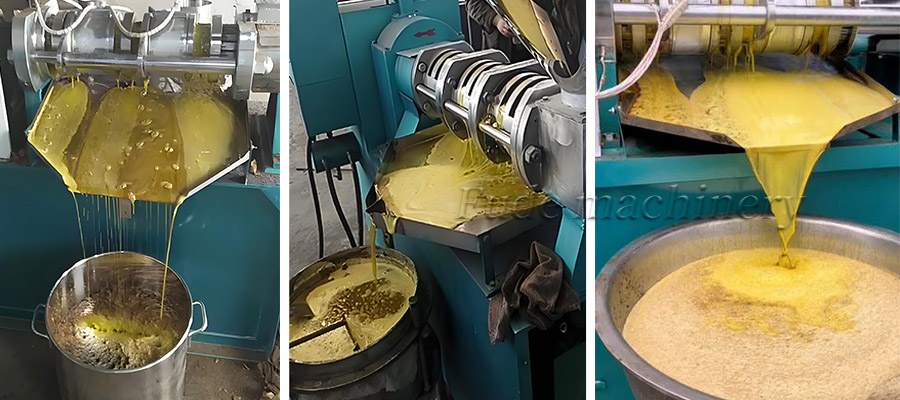
Is the Oil Cake Just Waste, or a Valuable By-product?
Thinking only about the oil yield? Discarding the press cake or selling it cheaply? Recognize that the oil cake (meal) often holds significant value that can boost overall profits.
The oil cake remaining after pressing is not waste. It’s typically rich in protein and residual oil, making it a valuable animal feed, organic fertilizer, or even a source for protein extraction. Maximizing its value is key.
A successful oil pressing business looks at the entire process, not just the primary product (oil). The solid residue left after oil extraction, known as oil cake or meal, is a significant by-product that often has considerable economic value. Ignoring or undervaluing the cake means leaving potential revenue on the table.
Composition and Uses of Oil Cake
The specific nutritional profile of oil cake varies depending on the original oilseed and the efficiency of the pressing process. However, it generally contains:
- Protein: Often the most valuable component, making it an excellent supplement for animal feeds (livestock, poultry, fish).
- Residual Oil: Provides energy content for feed. The level depends on the pressing efficiency (as discussed earlier).
- Fiber: Adds roughage to animal diets.
- Minerals: Contributes essential nutrients.
Common uses include:
- Animal Feed: This is the most widespread use. The high protein content makes it highly sought after by farmers and feed manufacturers. Market value often depends on protein percentage.
- Organic Fertilizer: Contains nitrogen, phosphorus, and potassium, making it a good soil amendment.
- Further Processing: In some cases, specific proteins or other compounds might be extracted for food or industrial applications.
- Biofuel: Lower value cake can sometimes be used as biomass fuel.
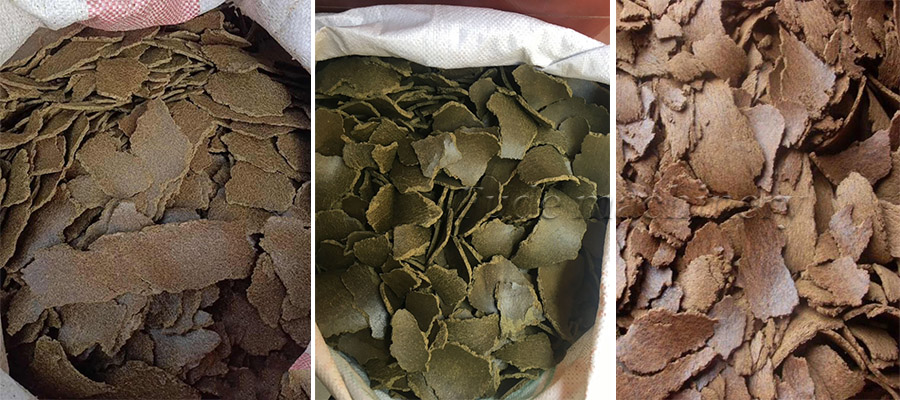
When is Standard Equipment Not Enough?
Processing unusual seeds or have unique quality goals? Finding off-the-shelf machines don’t quite fit? Consider if customization is not just a luxury, but a necessity for your project.
While standard screw oil presses are designed to handle common oilseeds like soybeans, rapeseed, sunflower, and peanuts effectively, the world of oils is vast. If you are working with less common raw materials or have very specific requirements for your final product or process, a standard machine might fall short.
The Value of Experienced Collaboration
Customization requires more than just assembling parts differently. It demands deep engineering knowledge and practical experience.
- Supplier Capability: Choose a manufacturer with a proven track record in R&D and custom projects. They need engineers who understand oilseed characteristics and pressing dynamics. As Zhengzhou Fude Machinery, with decades of experience and a dedicated R&D team, we have successfully delivered numerous customized solutions globally.
- Clear Communication: You must clearly define your raw material, process goals, and desired outcomes. Provide samples if possible.
- Iterative Process: Customization often involves discussion, design proposals, feedback, and potentially pilot testing.
- Cost and Time: Be prepared for potentially higher upfront costs and longer lead times compared to standard equipment. However, this investment can be crucial for achieving project viability and desired quality.
Don’t force a standard machine to do a job it wasn’t designed for. If your project involves unique elements, engaging with a capable manufacturer like us early on to discuss customization can be the key to achieving your specific operational goals.
Conclusion
Look beyond basic specs; success lies in details like temperature control, wear parts, pre-treatment, and realistic expectations. Choose partners who understand this.
Related recommendations
-
What are the advantages and disadvantages of hydraulic oil press
225What are the advantages and disadvantages of hydraulic oil press As a commonly used oil extraction equipment, hydraulic oil press has its unique advantages and disadvantages. Let me introduce it to you ,
View details -
What is an oil press
81How does the oil press work? Revealing the three mainstream technologiesSpiral pressing methodHydraulic pressing methodSolvent leaching methodIs cold-pressed oil really healthier?How to choose a suitable oil press for oneself?Widespread use of oil...
View details -
What is the difference between hydraulic oil press and screw oil press
324Zhengzhou Fude Machinery integrates research and development, manufacturing, and sales, deeply understands customer needs, recommends and answers equipment questions for customers, teaches operation techniques, and produces oil presses, refiners, ...
View details -
What are the advantages of an oil press
444Spiral oil press equipment is widely used in various fields such as obtaining plant seed oil and separating and extracting chemical raw materials. Such as sesame, peanut, rapeseed, olive, etc.
View details
HelloPlease log in